The goal of any high-purity water system is quite simple: Remove as many contaminants as you can, as easily and as economically as possible. The question is how ? As in any any challenge, ‘there are many tactical issues to consider. The first step is to analyze the source’s of the feed water. Consistency is a critical issue, especially if the source is surface, water, which may be subject to seasonal variation.
Removing particles, ionic impurities, and organic contaminants is important, but the biggest challenge facing pharmaceutical-grade water systems is removing bacteria and pyrogens and keeping them under control. And, it’s not simply a matter of running the water through a prescribed series of isolated treatment steps to theoretically meet the criteria. Bacteria can grow almost anywhere and eventually will multiply into numbers that would overwhelm any water treatment system.
USP standards for purified water & water for injection
Component | USPXXII | USPXXIII |
ph Chloride (mg/I) Sulphate (mg/I) Ammonia (mg/I) Calcium (mg/I) Carbon Dioxide (mg/I) Heavy Metals (mg/I) Oxidizable Substances Total Solids (mg/I) TOC Conductivity Bacteria (cfu/ml) Purified WFIv Endotoxin (Eu/ml) by LAL Purified WFI |
5.0 to 7.0 0.5* 1.0* 0.03* 1.0* 5.0* 0.1 as Cu* Pass USP Permanganate Test 10.0 ---- ---- 100** 50 ---- 0.25 |
Unchanged Eliminated+ Eliminated+ Eliminated+ Eliminated+ Eliminated+ Eliminated Eliminated++ Eliminated+ 50 ppb 1.25 uS/cm 100 0.1 Unchanged Unchanged |
*Numerical values are interpretations of procedures listed in the Standards in United States Pharmacopoeia XXII edition.
** Guideline only.
+ Replaced by conductivity measurement.
++ Replaced by TOC measurement
The harsh reality is that different components of a water purification system do not operate independently of one another. Depending on the system, it may be critically important to know how the diggerent treatment steps can affect one another. The most difficult concept to grasp may be that every phase of the process has the potential to not only remove certain contaminants, but to add others. Finally, there’s the issue of compliance. Whatever their needs, pharmaceutical manufacturer need water purification systems that produce consistent, reproducible results that are easily validated.
PRODUCING PHARMACEUTICAL-GRADE WATER
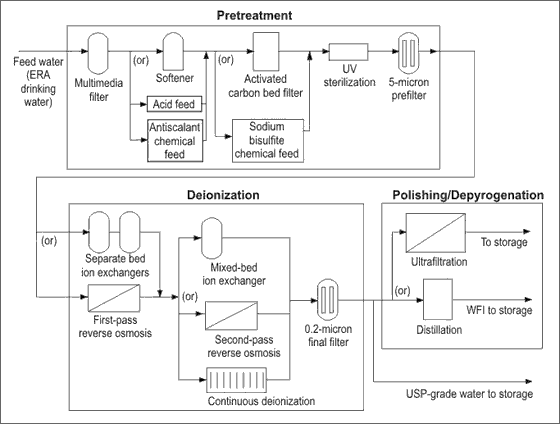
Figure 1. The typical treatment system design for producing pharmaceutical-grade water
demonstrates that there's more than one way to produce USP water, as can be seen by
the options in this schematic incoming water quality and the needs of the manufacturing
process will dictate which steps are most appropriate.
The parts of Typical System :
1. Primary filtration. Multimedia or sand filters remove particles larger than 5 microns from incoming feed water. If there are high levels of iron, greensand filters are needed. bacteria risk is minimal of chlorine residual is maintained and the filter is back-washed regularly.
2. Softening. Softening removes hardness and trace metals that would otherwise form scale on downstream equipment (particularly detrimental to reverse osmos. membranes). This step also eliminates the need for acid addition to control scale, so a downstream reverse osmosis system can reject a higher percentage of bicarbonate. bacteria risk is minimal if chlorine residual is maintained. Because a carbon filter removes chlorine, in most pharmaceutical water system designs, the softener is typically placed a head of it.
3. Activated carbon filtration Carbon filters can reduce TOC levels to below 1 ppm (part per million), remove 1- to 5-micron particles, and reduce chlorine to sub-ppm levels. This is particularly important if there are any composite menbranes downstream. Bacteria risk is high, because the lower part of the carbon media can be a bacteria breeding gorund. Therfore, it is absolutely essential to include provisions for frequent hot water or steam sanitization procedures, which will control bacteria growth.
4. Primary chemical treatment. Acids such as HCL and SO4 neutralize alkaline waters; NaOH neutralizes acidic waters and converts carbonates and bicarbonates into CO2. Ozone can slo be injected to control bacteria. Antifoulants keep marginally solubale salts from forming scale on system components. Instead of a carbon filter, sodium bisulfite may be added to dechlorinate the water. Bacteria risk is low to moderate. But, remember that any added substance can be considered a contaminant and must eventually be removed. Furthermore, sodium bisulfite solution must be produced frequently to avoid bacteria growth in the solution.
5. Ultraviolet (UV) sterilization. UV radiation reduces viable bacteria levels and cuts TOC to parts-per-billion (ppb) levels in high purity water. UV can also be used to remove residual ozone that has been used as a sanitizing agent. Ultraviolet sterilizers should not be used to remove large bacteria concentrations. The accompanying dissociation of TOC into ions can degrade water quality. Bacteria risk is minimal, provided the lamps function properly and are replaced regularly.
6. Reverse osmosis (RO). RO uses semi-permeable membranes to remove upto 95 percent of the dissolved ions, organics, bacteria, and pyrogens. It can significantly reduce the volume of chemicals reduce the volume of chemicals used in water purification systems, that normally reject about 25 percent of their feed water as waste. The first pass of an RO system is often considered pretreatment to a further deionization step-eityher continuous deionization, second-pass RO or ion exchange. During RO, bacteria risk is low to moderate. It can be minimized with proper sanitary design, regular effective sanitization, and optimum pretreatment. But, because most RO used in pharmaceutical applications requires dechlorinated water, it is possible for bacteria to collect and grow in the system, especially during extended shutdown periods. Additionally, selection of RO membranes must be based not only on the types and concentrations of contaminants to be removed, but also on their compatibility with cleaning chemicals. For instance, cellulose acetate (CA) RO membranes are generally more resistant to chemical cleaning, but have relatively low rejection rates. Polymeric thin-film polyamide and composite RO membranes have composite RO membranes have higher rejection rates, but are more sensitive to chemical degradation, particularly from chlorine-containing chemicals.
7. Ion exchange (demineralization). Ion exchange systems replace ionic contaminants with more “compatible” H+ and OH- ions. There are three different type of systems: cation, anion, and mixed-bed. cation exchangers replace cationic (positevely charged) contaminants such as sodium, calcium and magnesium ions with H+ ions. Anion exchangers replace anionic (negatively charged) contaminants such as chloride and sulphate with OH- ions. And, mixed-bed exchangers do both. Thesed resin-based treatment methodes, however, do not offer a barrier that actually removes organics, ions, bactria and pyrogens. Demineralizers are resonably tolerant to improper operation. This major disadvantage is the need to handle acid or caustic. Bacteria risk is minimal with proper design of piping and valves, regular regeneration (often before exhaustion) and proper pre-treatment. The regeneration process can be used to sanitize the system, but it need to be done frequently.
8. Continuous deionization (CDI). This is a relatively new technology which has gained wide acceptance. CDI avoids many of the problems associated with ion exchange and even produces higher quality water than a secon-pass RO system. The patented CDI process uses a combination of ion exchange membranes, ion exchange resins, and electricity to produce high-purity water continuously and without the need for hazardous chemicals. It uses electricity instead of acid and caustic to continuously regenerate the resins and produces consistent, high-purity water. In pharmaceutical applications, CDI is normally used as a polishing step after RO and is capable of producing upto 18 megaohm water. CDI systems can operate
with 95 percent water recovery by recirculating the reject stream. Like ion exchange, CDI does not rely on a membrane barier and, therefore, is limited in its ability to remove organics, bacteria and pyrogens. Bacteria risk is minimal with proper design, frequent operation, regular sanitization, and adequate pretreatment.3
9. De-pyrogenation for WFI. The system components described up to this point can generally be used in systems that produce both USP-grade and WFI-grade water. But to meet the official WFI-grade water specifications (as specified in USP 23), a de-pyrogenation step is required. In the pharmaceutical industry, distillation, which is very effective in killing bacteria and removing pyrogens, has long been the standard method for producing water for injection. But this has begun to change, in part, because of the high operating costs associated with this energy-intensive operation. Furthermore, distillation processes require significant pretreatment equipment to protect them from scaling and corrosion-usually carbon filtration, sodium sulfite addition (dechlorination) and deionization. RO has also been used as a de-pyrogenation step, but hasn’t been nearly as well accepted, because it is generally perceived to have operating temperature limits too low to control bacterial growth. The temperature limits on these polymeric based membranes also preinclude the use of steam-in-place (SIP) sterilization procedures, another widely used technique in the pharmaceutical industry.
10. Ultrafiltration (UF). Is a membrane process that can produce highly purified water at a continuous rate equal to about 95 percent of the incoming feed water. It is similar to reverse osmosis, except that it does not remove dissolved ions. but it can be used to remove bacteria, pyrogen-free USP-grade water. Furthermore, recent tests on a Membralox ceramic-based UF system revealed that this type of memebrane (starting with DI water that has passed through a 2.0 micron prefilter) is able to remove pyrogens to levels that meet WFI criteria, Significantly, ceramic membranes can be used at high temperatures and pressures, so they can be easily sterilized with steam.